Meiko Technology 01
金型設計から完成品まで、
確かな品質と信頼の一貫生産体制
業界の常識を覆す新たな挑戦
設計から完成品まで一貫生産体制で対応!金型設計・製作・メンテナンスから、カシメ・研磨などの後工程、さらに熱処理やメッキなど外注工程も包括し、お客様の手を煩わせることなく完成形で納品します。高品質・迅速・柔軟対応を実現し、納期短縮やコスト削減に貢献いたします。
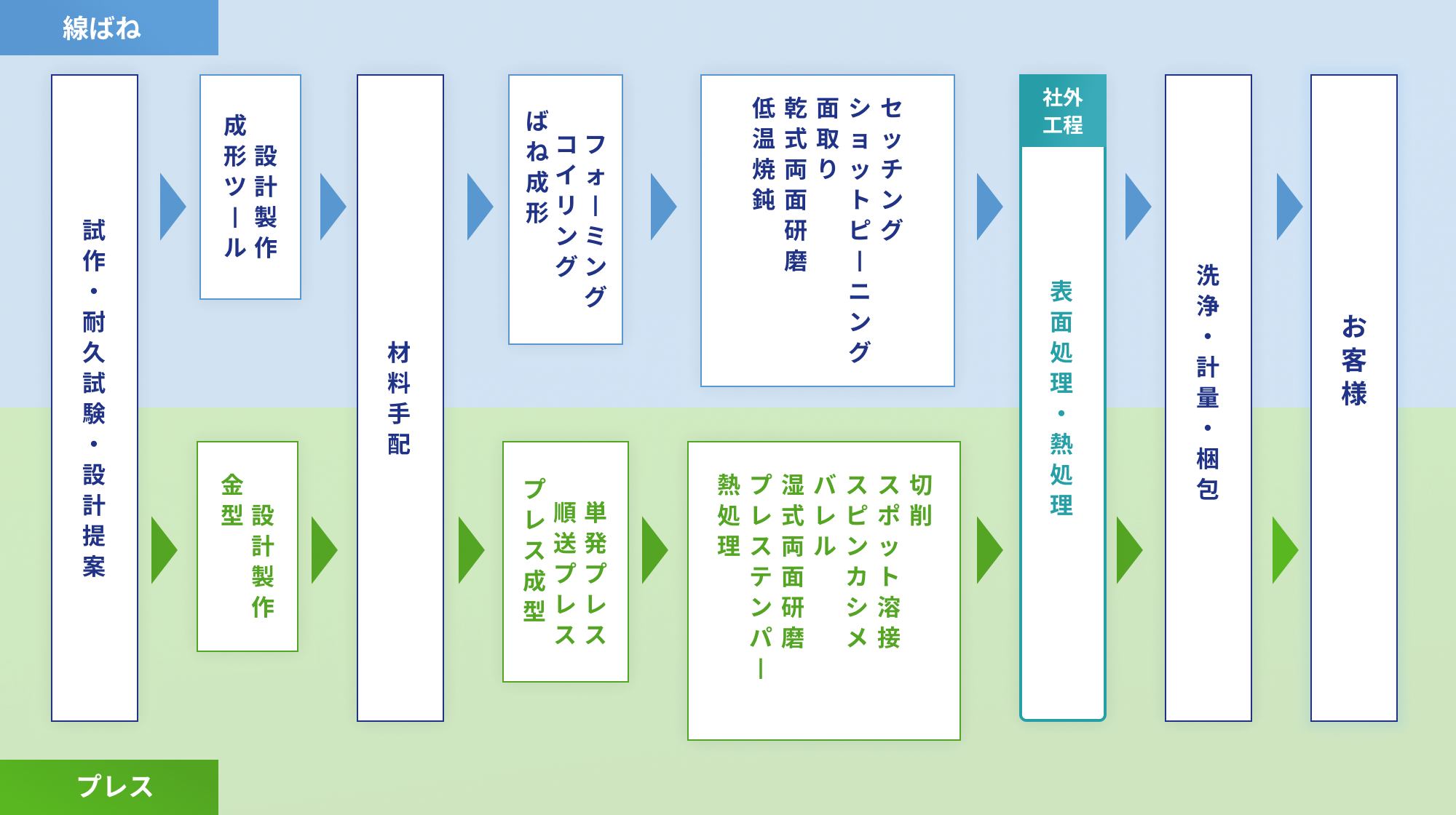
1. 金型設計・製作・メンテナンス
高精度な金型設計から、製作、メンテナンスまで自社内で対応。
2. 後工程の対応
カシメや研磨といった製品仕上げも内製化。外注先を活用した熱処理・メッキなどの工程も含め、スムーズな一貫対応。
3. 高負荷の加工条件下でもツール寿命を維持し、原価低減を実現。完成形での納品
お客様の手を煩わせず、完成品として納品可能。納期短縮と品質保証を実現。
Meiko Technology 02
「全せん断加工」による
原価低減
汎用プレスで
高精度&低コスト加工に挑戦
従来の全せん断加工工法では、ファインブランキングが採用されてきました。この工法は高精度な加工が可能である一方、専用設備の導入・運用コスト・金型費用が高くなるという課題がありました。MEIKO独自の特殊な金型部品加工技術により、汎用プレスを活用した全せん断加工金型の開発が可能となり、これにより原価低減効果を実現しています。
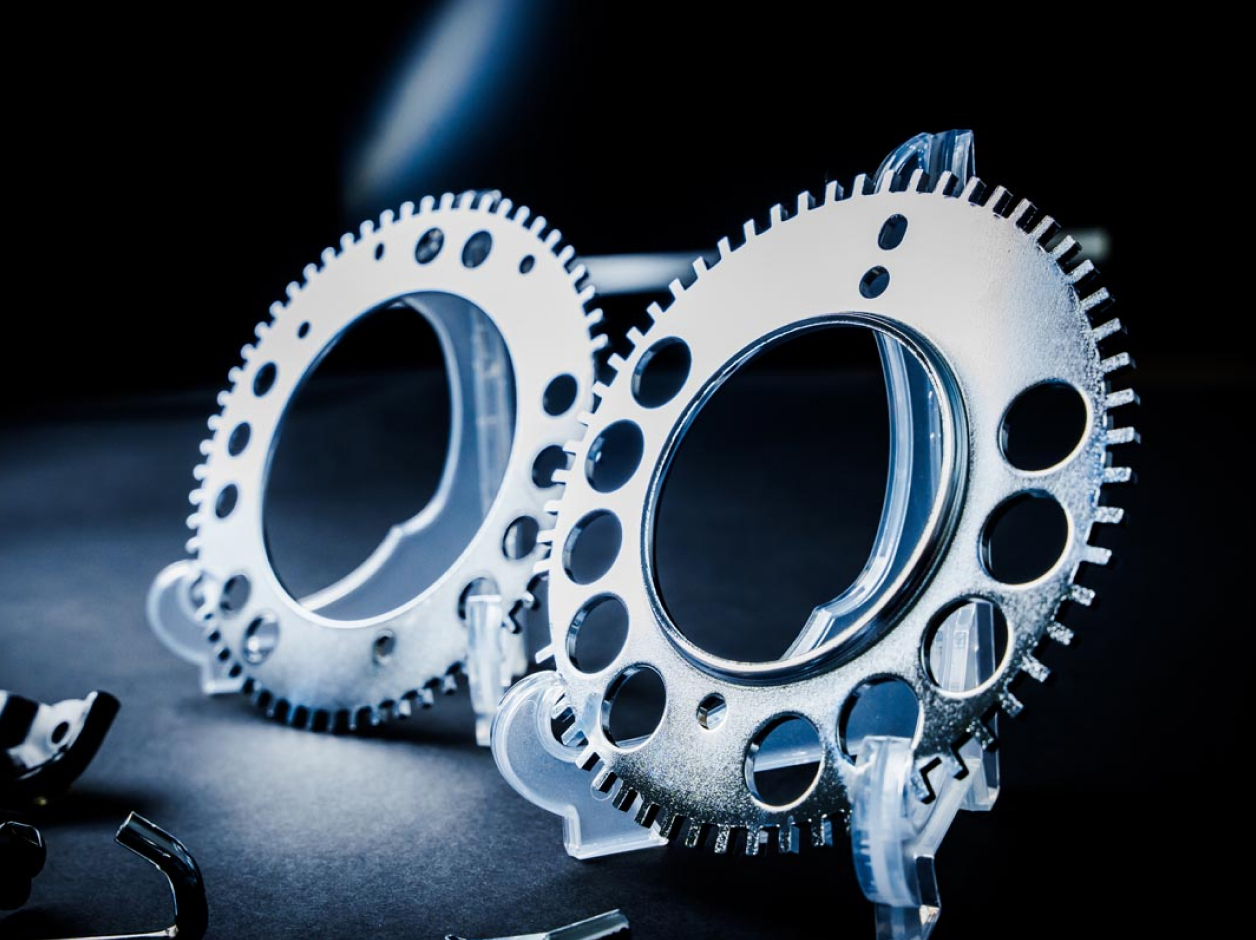
1. 専用設備の不要化
ファインブランキング用の専用設備が不要となるため、初期設備投資を大幅に削減できます。
2. 加工コストの低減
汎用プレスを使用することで、運用コストの削減が可能です。
3. 金型コストの最適化
金型部品加工技術の進化により、低コストで高耐久の金型が製作可能になっています。
4. 生産性の向上
汎用プレスによる高速加工が可能なため、生産サイクルタイムを短縮し、量産効率を高めます。
高品質な仕上がり
ファインブランキングに匹敵する加工精度を実現。
柔軟な適用性
幅広い製品形状に対応可能。
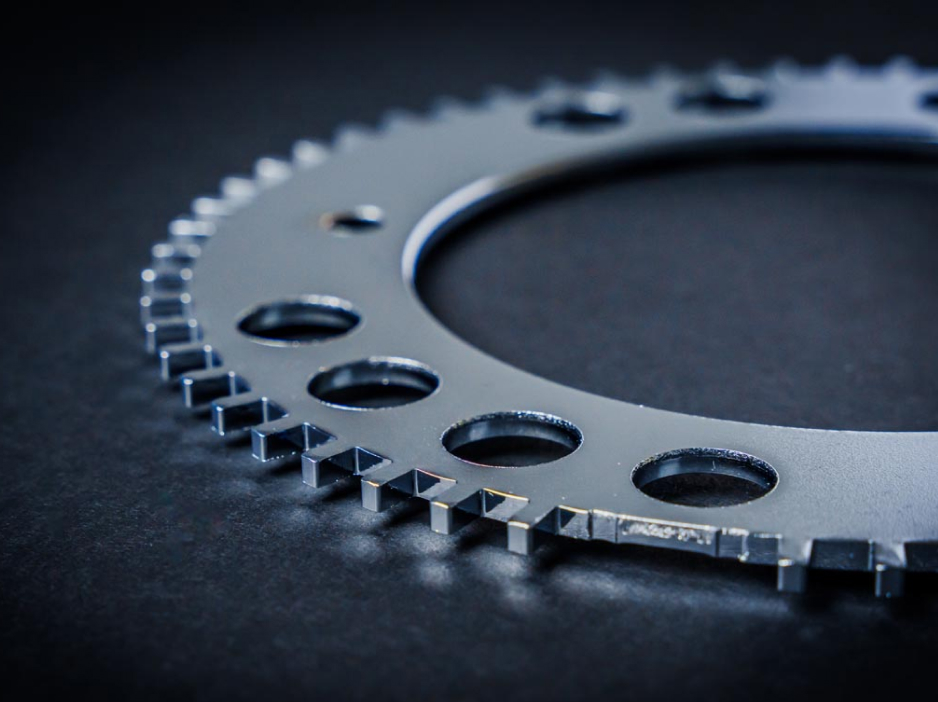
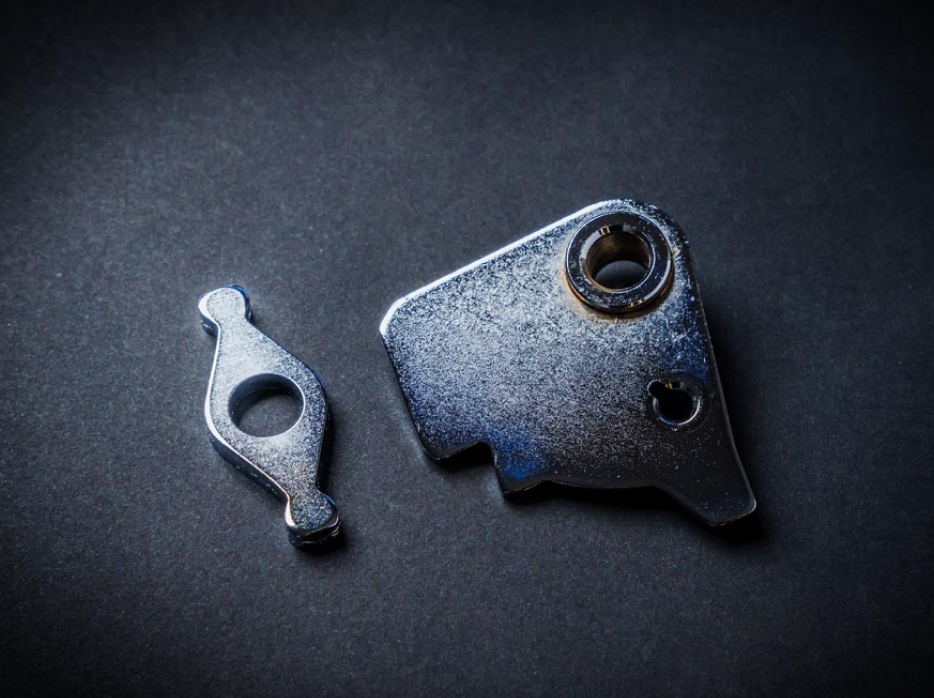
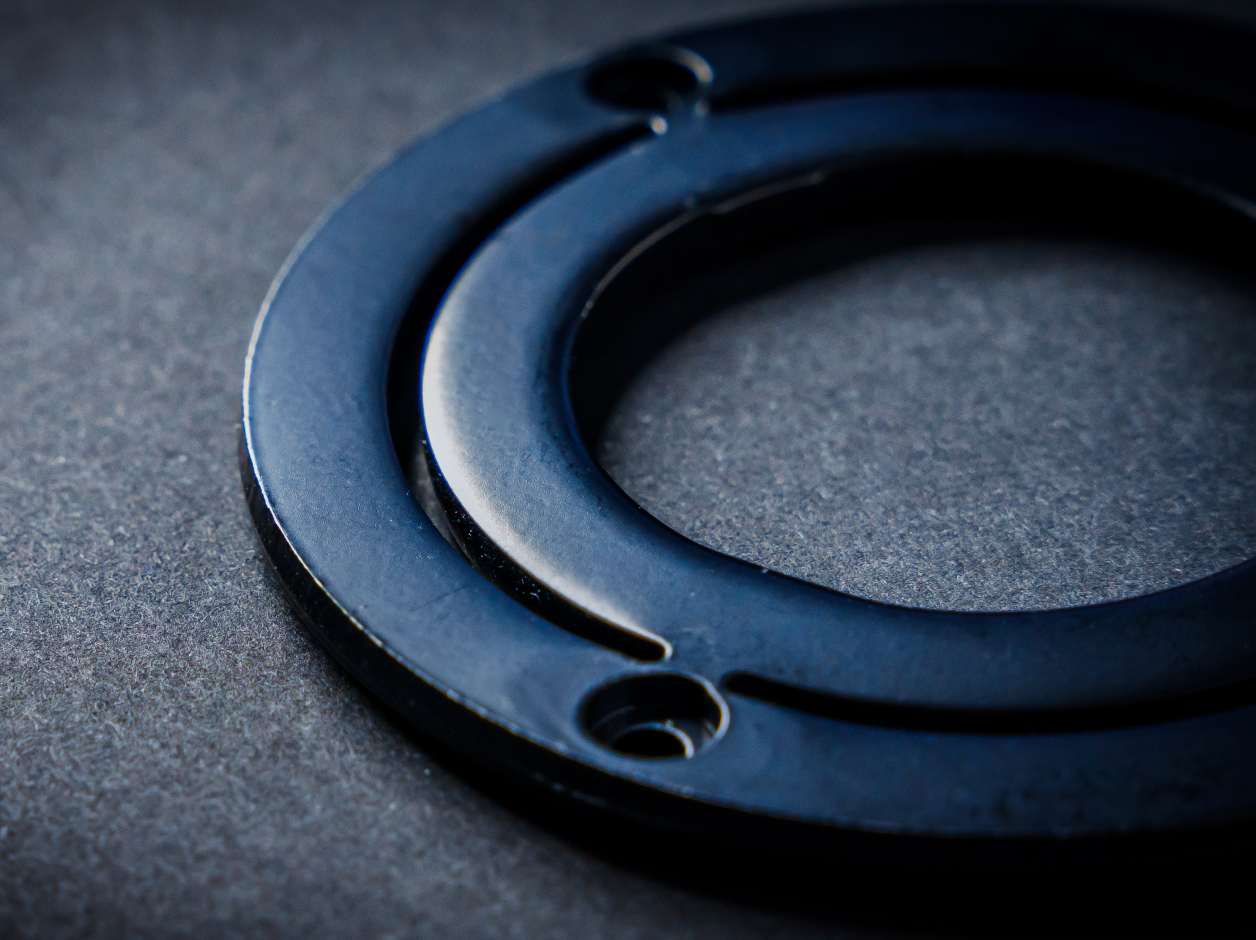
Meiko Technology 03
板厚の限界を超えた
高精度打抜き技術
業界の常識を覆す新たな挑戦
一般的に、打抜き孔加工では「板厚の1.5倍程度が限界」と言われています。しかし、弊社では独自の技術開発により、この限界を突破しました。従来の加工法では実現が難しかった「板厚1/2幅の細溝打抜き孔加工」を可能にしました。
1. 特殊設計の抜きパンチの開発
独自に設計・製造した抜きパンチを採用し、精密加工を実現しました。
2. 加工コストの低減
高負荷の加工条件下でもツール寿命を維持し、原価低減を実現。
3. 加工プロセスの最適化
打抜き工程を見直し、高度な制御技術を組み合わせることで、板厚1/2幅の細溝孔加工を実現。
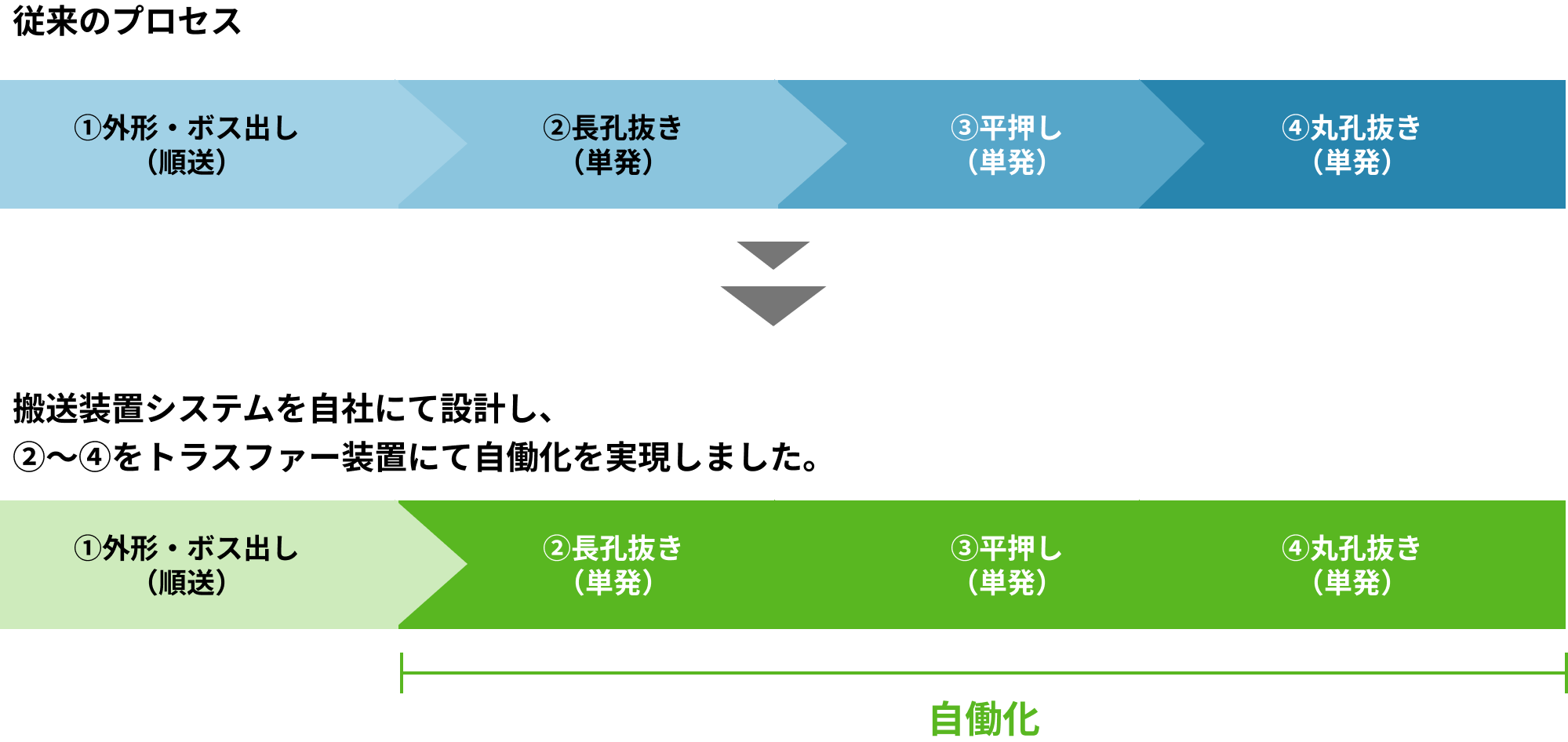
製品紹介:T社エアコン部品
材質 | SPHC |
板厚 | 4.3mm |
細溝幅 | 2.0mm |
生産数 | 80,000(個/月) |
要求品質
溝幅公差 | SPHC |
ボス形状 ①位置度 ②裏側膨らみ |
φ0.2 以下 0.3mm 以下 |
平面度 | 0.2mm 以下 |
パンチ耐久性向上 | 立上げ時 現在 300,000個で摩耗交換 |
3,000個で折損
Meiko Technology 04
原価低減×生産効率向上
を実現する
マルチフォーミング
加工技術
高効率・高歩留りの革新的加工技術
弊社のマルチフォーミング加工は、材料の無駄を削減しつつ、複雑な形状にも対応可能な次世代加工技術です。短い段取り時間と高精度な加工により、原価低減と生産効率向上を同時に実現します。
1. 材料ロスを最小限に抑える高歩留り
材幅を活用して成形することで、スクラップの発生を大幅に削減。銅やアルミなど高価で幅広い材料に対応し、特に高価な材料においては他を寄せ付けない材料ロス低減に貢献可能。
2. 段取り時間の大幅短縮
サーボモータ駆動により、稼働部品の段替えが容易。段取り時間を従来の1/4(約4時間→約1時間)に短縮。
3. 1工程で複雑形状を実現
プレス加工で数工程を要していた複雑な形状も、1工程で対応可能。最大50%の原価低減を実現。
4. サーボモータ駆動による柔軟性
高精度な動作制御が可能で、多様な製品形状に対応。段取り変更の負担が軽減され、小ロットや多品種生産にも最適。
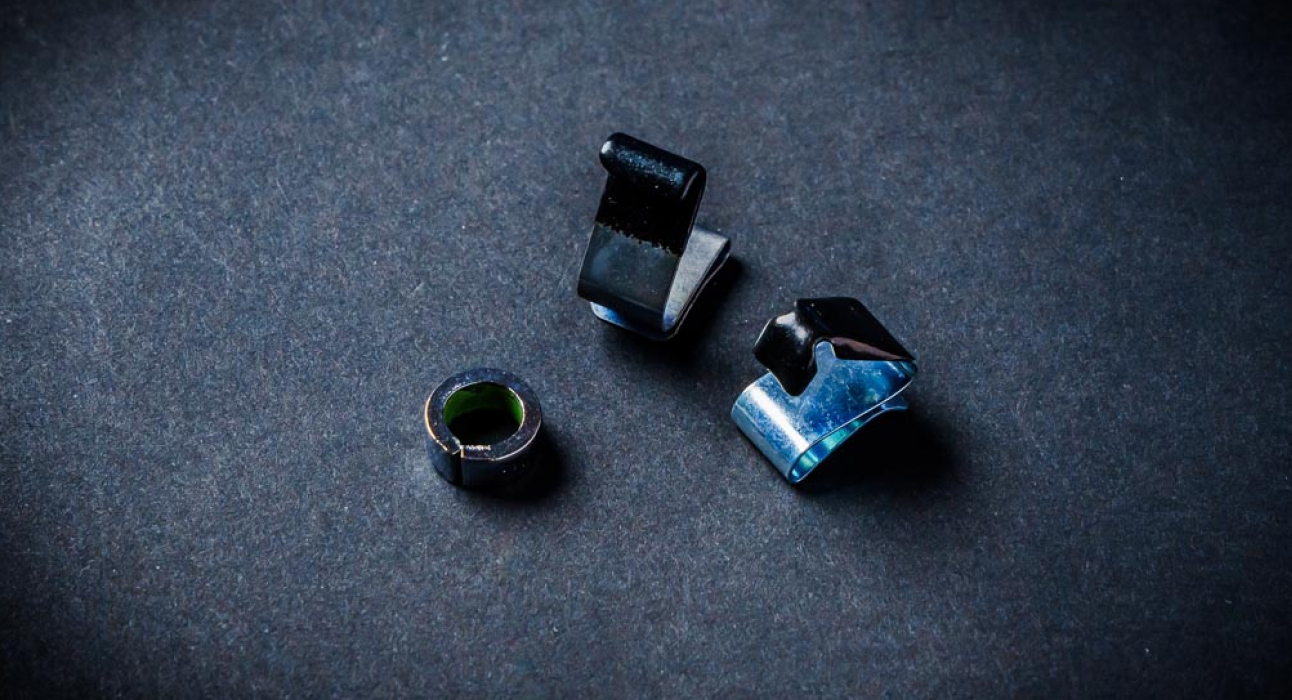
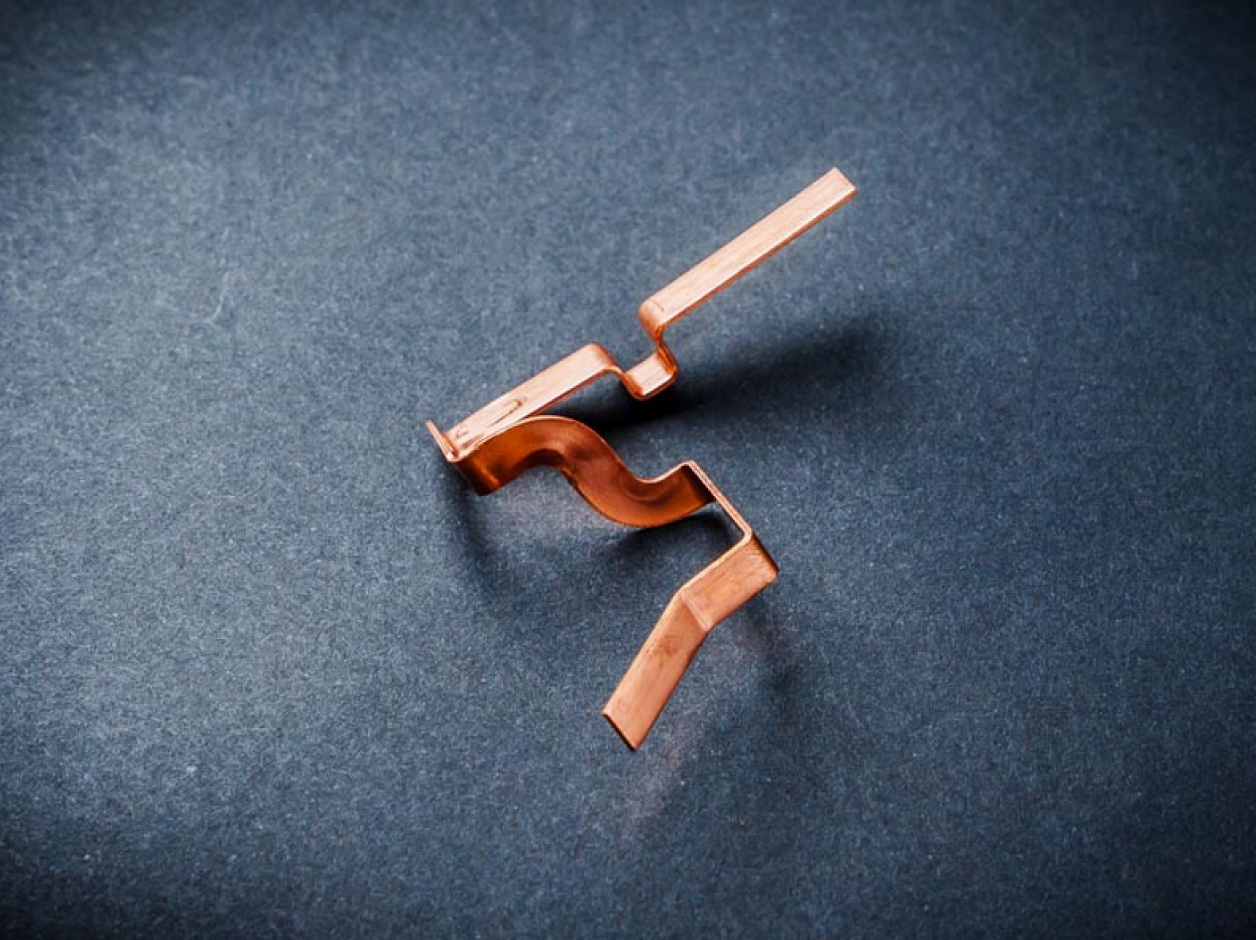
弊社のマルチフォーミング加工は、材料の無駄を削減しつつ、複雑な形状にも対応可能な次世代加工技術です。短い段取り時間と高精度な加工により、原価低減と生産効率向上を同時に実現します。銅材を使用したバスバー加工において、マルチフォーミング技術により材料ロスを大幅に削減し、効率的な製造を実現。
エッジワイズ加工を活用することで、従来困難だった形状も対応可能。これにより、コスト削減と環境負荷軽減を同時に達成し、特に高価な銅材を使用した製品において大きなメリットを提供します。
1. 材料ロスの大幅低減
材料幅=製品幅での加工が可能なため、余剰な材料を排除し、効率的な加工を実現。「エッジワイズ加工」により、従来難しかった材料幅側への曲げが可能。これにより、さらなる材料ロスの削減に貢献。
2. コスト効率と環境貢献
特に銅材の加工において、大幅なコスト削減が可能。材料削減によるCO2排出量の削減にも寄与し、持続可能な製造をサポート。
3. 「バスバー」製品への大きな貢献
銅材を使用した「バスバー」の加工において、効率性とコストパフォーマンスを向上。高精度かつ材料を無駄にしない加工が求められる分野で大きな付加価値を提供。
4. 多様な対応力
プレス加工では対応が難しい複雑な形状や特殊な設計にも柔軟に対応可能。
公差の調整が必要
1工程ごとの曲げの積み重ねにより、公差の拡大が発生する可能性。設計段階からの入念な調整をサポートし、精度の高い製品づくりを実現。
Meiko Technology 05
ロボットを活用した
ライン設計と
構築による原価低減
自動化×効率化
=ロボットが創る新たな製造のカタチ
弊社では、ロボットを活用したラインの設計から構築までを自社内で一貫して行う体制を整えております。
また、弊社は選別機等の簡易な設備の設計・製作も可能なため、柔軟で低コストなライン構築を実現いたします。これにより、短期間での導入および迅速な稼働開始が可能です。
1. 無人稼働による省人化
設備メーカーと協力し、これまで人手が必要だった作業を自動化。ロボットの活用によって作業人員を大幅に削減しております。
2. 工程連結による効率化
弊社独自の自動化工程設計とメーカーとの共同技術により、個別工程をロボット技術で効率的に連結。これにより作業フローを最適化し、稼働時間短縮や品質安定化を実現します。
3. 原価低減
効率化と省人化に加え、ロボット技術を用いた長期的なメンテナンスコスト削減や不良品削減を実現。これにより、直接的な製造コストを削減し、高い経済効果を生みます。
ロボットを活用した自動化の工程設計により、設備メーカーと連携して柔軟かつ高効率なライン構築を実現できる点です。この取り組みにより、製造現場の課題を包括的に解決し、クライアントの競争力向上に貢献いたします。
Meiko Technology 06
簡易設備が実現する
低コスト・高効率なライン構築
低コストで効率アップ!簡易設備のトータルソリューション
弊社では、選別機や自動箱替機などの簡易設備の設計から製作までを自社内で一貫して対応しております。短期間での設計・製作が可能で、導入後もスムーズな稼働を実現。また、簡易設備の設計・製作を担う専門人材が社内におり、人材育成にも力を入れているため、継続的な技術の進化を図っています。
1. 安価なライン構築
自社製作による簡易設備の導入により、初期投資を抑えつつも高品質な製品を提供。短納期で柔軟な対応が可能です。
2. 原価低減への貢献
簡易設備を活用して生産プロセスを最適化することで、ランニングコストやエネルギー消費を削減。効率的な生産を実現できます。
3. 柔軟なカスタマイズ対応
各工程のニーズに応じたオーダーメイド設備の設計が可能です。社内の専門スタッフが対応し、独自の生産条件に最適化されたライン構築を実現しております。また、現場で活躍するスタッフの技術力を高めるための教育を実施し、技術の持続的な向上を目指します。
「コストを抑えながらも高品質で柔軟性のある生産ライン構築」を追求し、人材育成と技術開発を実現します。
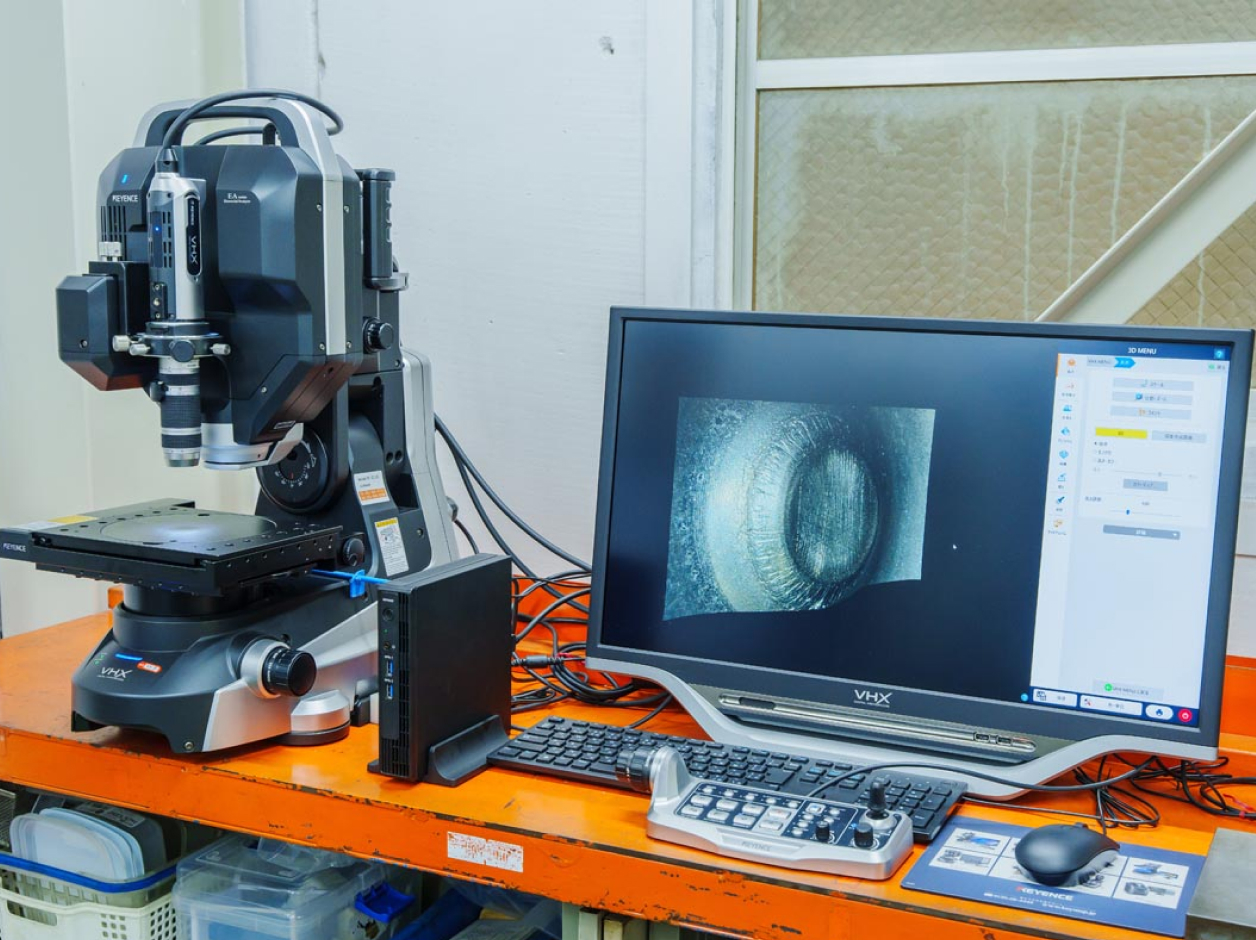
Meiko Technology 07
最先端の技術で、
品質に革新を、
名興発條の品質管理
品質管理における弊社の取り組み
弊社は製品の精度向上、トラブルの未然防止、迅速な問題解決を可能にしています。今後も継続的に設備の更新と技術の向上を図り、お客様に信頼いただける品質を提供し続けます。
1、測定について
弊社では、ばねの品質管理を徹底するため、測定室と同様の測定機を現場にも設置しています。これにより、現場においても高精度な測定が可能となり、測定誤差を最小限に抑えています。
また、主要な仕入先にも同様の測定機を設置することで、測定データの共有と迅速な対応を実現しています。この仕組みにより、供給チェーン全体での品質保証を強化し、信頼性の高い製品をお届けしています。
2、コンタミ管理・元素解析
コンタミネーション(異物混入)の管理に特化し、簡易的に元素解析が可能な顕微鏡を完備しています。これにより、ブレーキ部品のばねを含む重要部品の異物検査を迅速かつ精密に行っています。
この取り組みは、安全性が特に重要視される部品において、品質トラブルの未然防止に大きく貢献しています。
1、非接触の3次元測定機
高精度な3次元測定を可能にし、製品の寸法検査を短時間で実施しています。この装置は、複雑な形状の製品でも接触による影響を避けつつ、正確な寸法を測定できるのが特徴です。
2、まるごと3Dスキャン測定機
製品全体の3Dスキャンを行い、形状データを詳細に取得します。このスキャンデータは、過去の測定データやCADデータと比較することで、設計との微細な違いを把握し、製品の精度向上に役立てています。また、大型部品や複雑形状の検査にも対応可能です。