Meiko Technology 01
A reliable, consistent production system with assured quality from mold design to finished product
A new challenge that overturns conventional wisdom in the industry
We offer a consistent production system from design to finished product! We handle everything from mold design, production, and maintenance to post-processing such as crimping and polishing, as well as outsourced processes such as heat treatment and lating,delivering the finished product without bothering the customer. We achieve high quality, speed, and flexibility, and contribute to shortening delivery times and reducing costs.
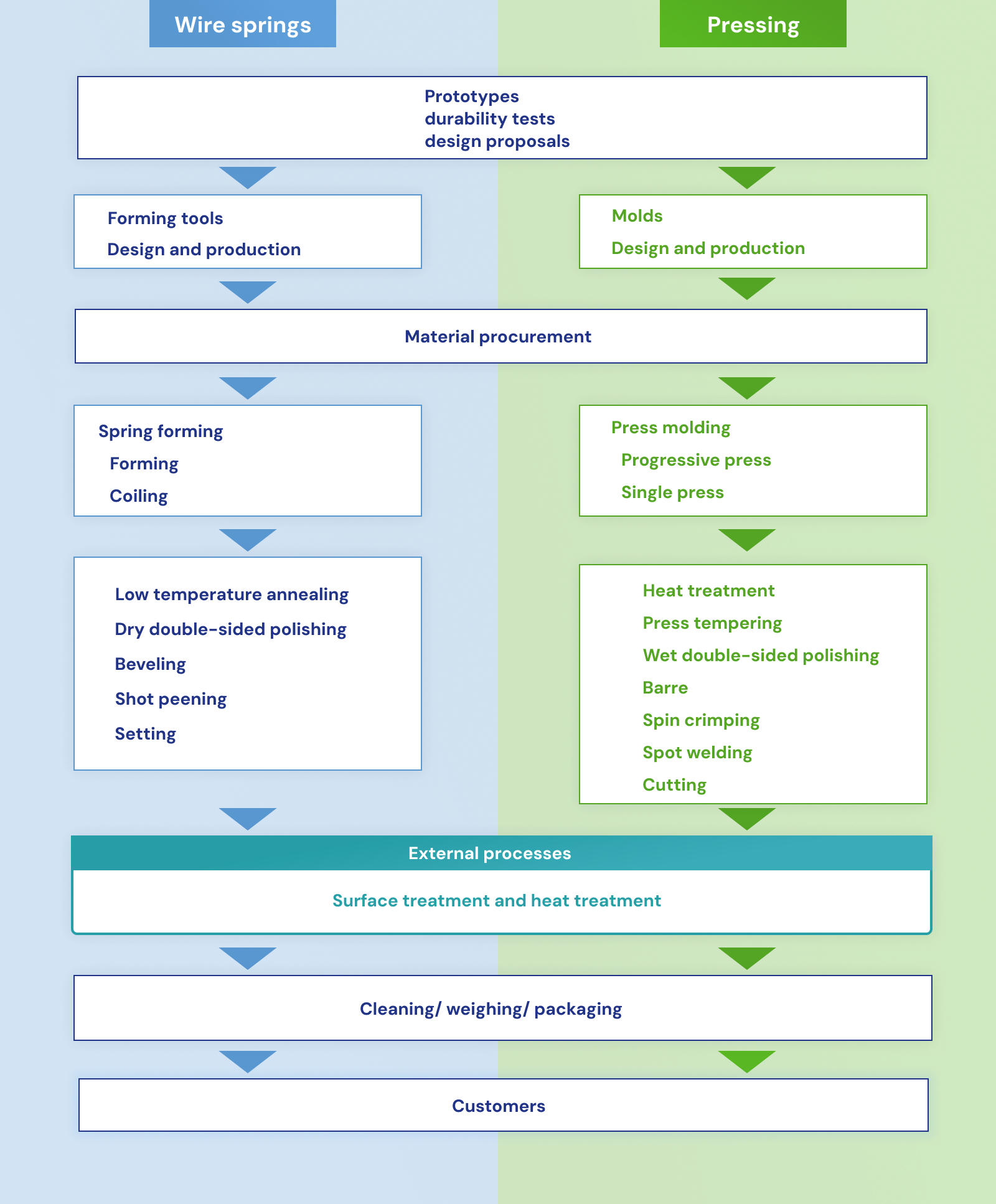
1. Mold design, production, and maintenance
We handle everything from high-precision mold design to production and maintenance in-house.
2. Post-process support
Product finishing such as crimping and polishing is also done in-house. We provide smooth, consistent support, including processes such as heat treatment and plating using outsourced companies.
3. Maintains tool life even under high-load processing conditions,reducing costs. Delivery in finished form
We can deliver finished products without bothering the customer. We achieve shorter delivery times and quality assurance.
Meiko Technology 02
Cost reduction through
"full shear processing"
Challenging high-precision, low-cost processing with a general-purpose press
Fine blanking has been used in conventional full shear processing methods. While this method allows for high-precision processing, it has the problem of high installation and operating costs for dedicated equipment and high mold costs.MEIKO's unique special mold part processing technology has made it possible to develop full shear processing molds using general-purpose presses, thereby achieving cost reduction effects.
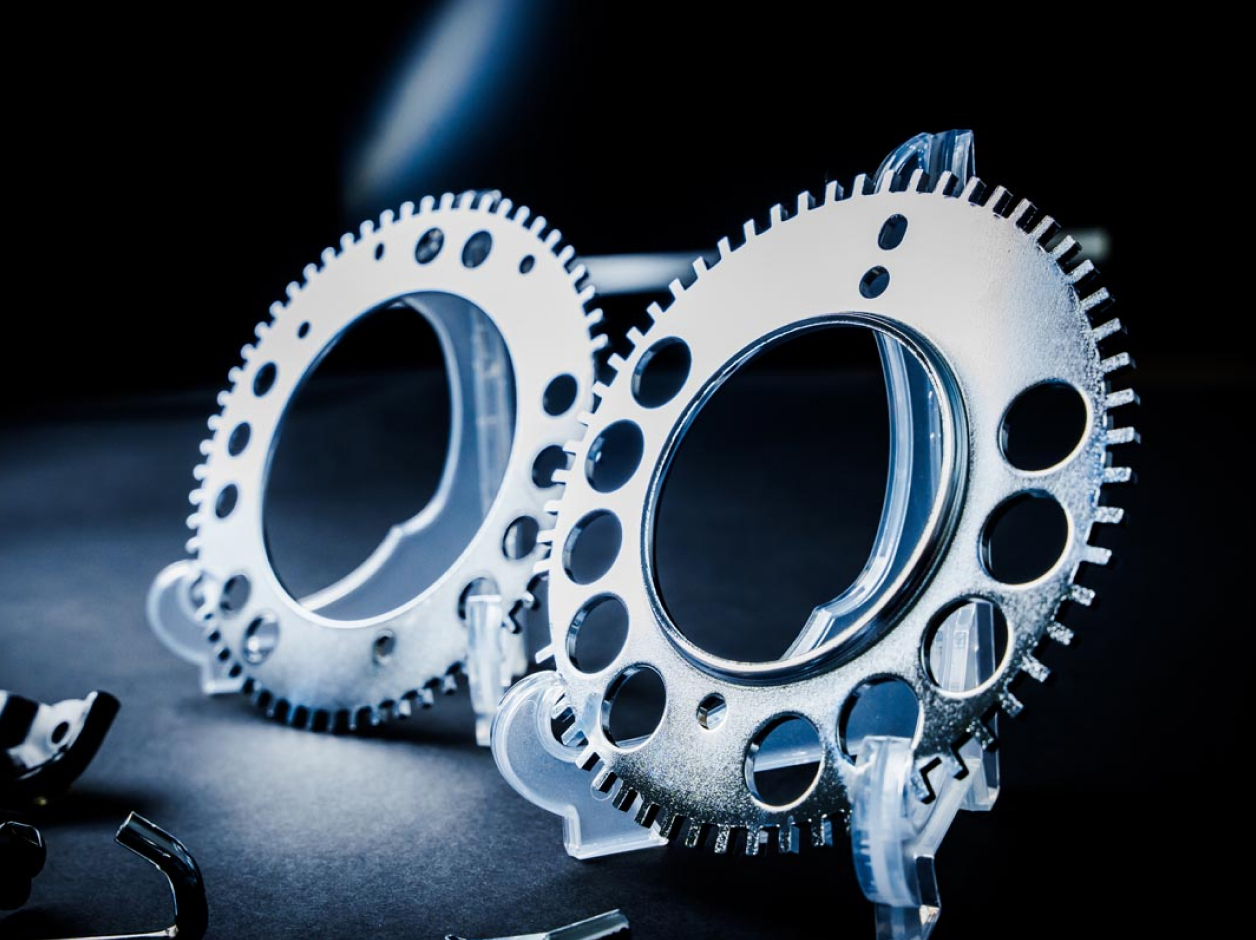
1. Elimination of the need for dedicated equipment
Since dedicated equipment for fine blanking is no longer necessary, initial capital investment can be significantly reduced.
2. Reduction in processing costs
Using a general-purpose press allows for reduced operating costs.
3. Optimization of mold costs
Due to the evolution of mold part processing technology, it is now possible to manufacture highly durable molds at low cost.
4. Improved productivity
High-speed processing is possible using a general-purpose press, shortening production cycle times and improving mass production efficiency.
High-quality finish
Achieves processing accuracy comparable to fine blanking.
Flexible applicability
Can handle a wide range of product shapes.
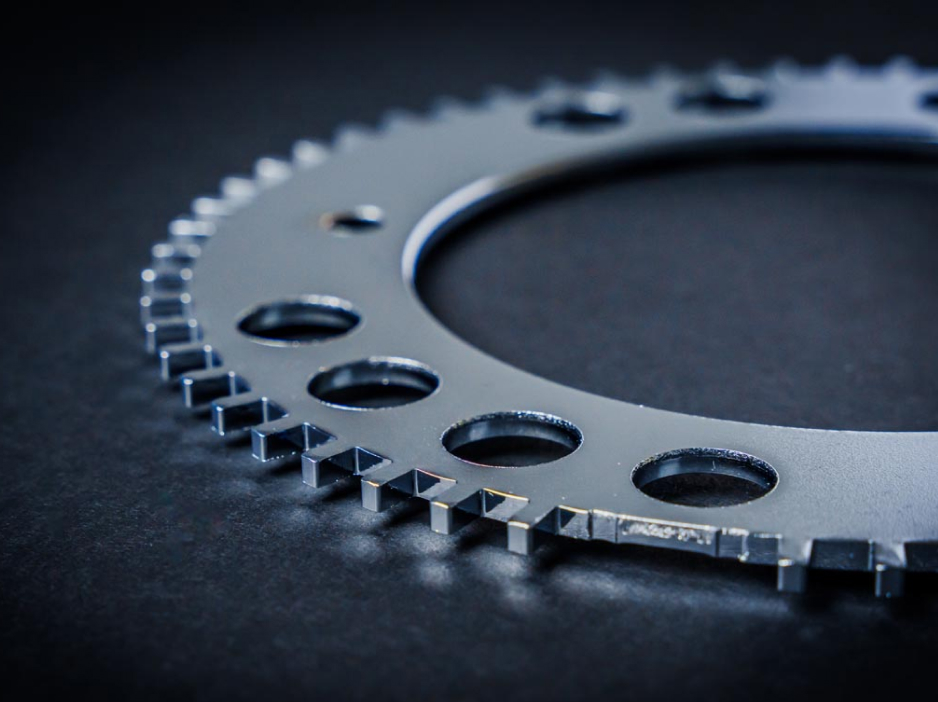
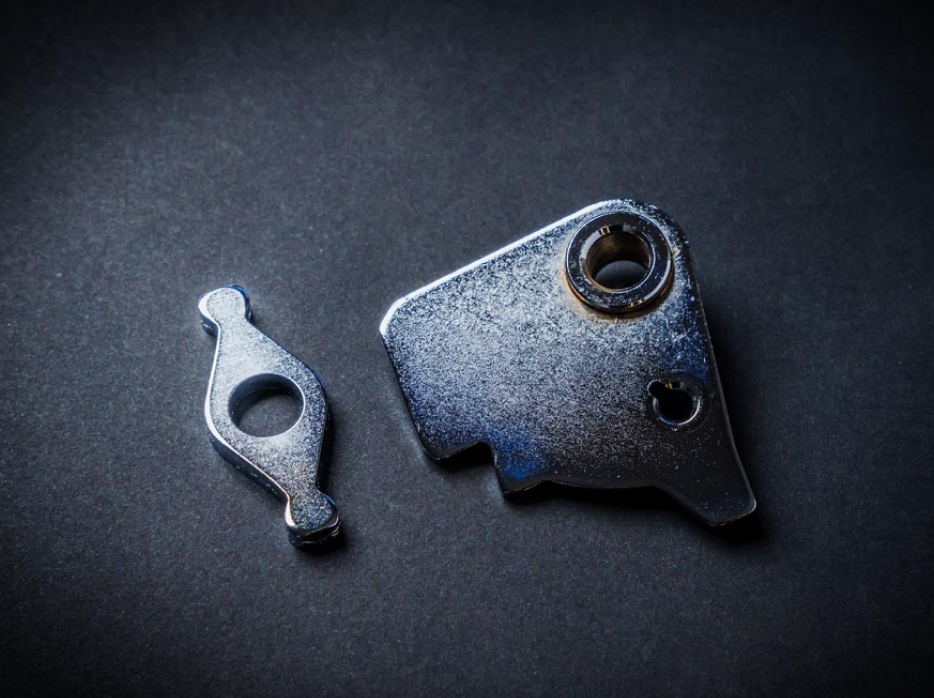
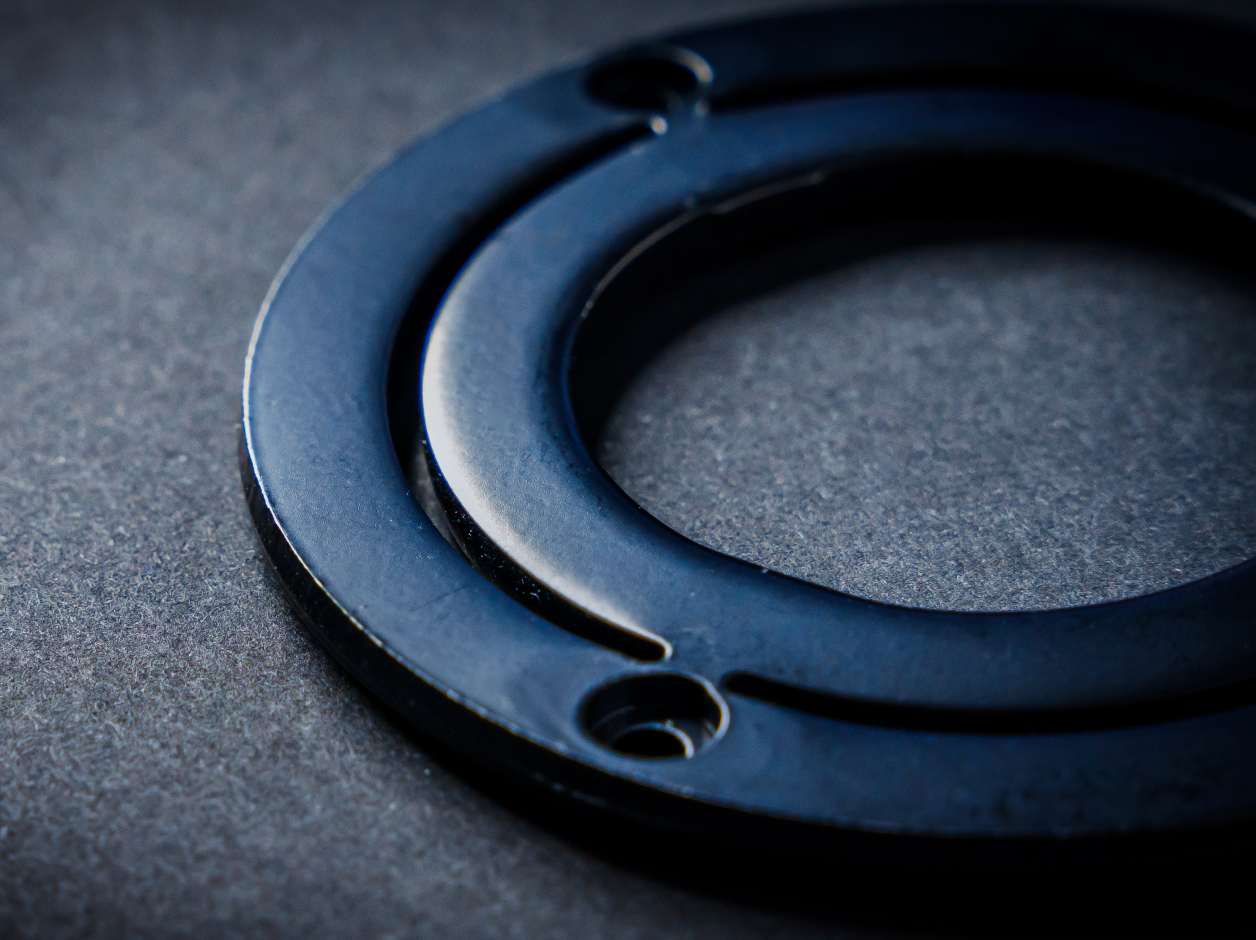
Meiko Technology 03
High-precision punching technology that exceeds the limits of plate thickness
A new challenge that overturns industry common sense
In general, it is said that the limit for punching hole processing is about 1.5 times the plate thickness.However, our company has broken through this limit through its own technological development. We have made it possible to process fine groove punching holes with a width of 1/2 the plate thickness, which was difficult to achieve with conventional processing methods.
1. Development of specially designed punching punches
We have achieved precision processing by adopting punches that we designed and manufactured ourselves.
2. Reduced machining costs
Maintains tool life even under high-load machining conditions, realizing cost reduction.
3. Optimized machining process
By reviewing the punching process and combining it with advanced control technology, we have achieved fine groove hole machining with a width of 1/2 the plate thickness.
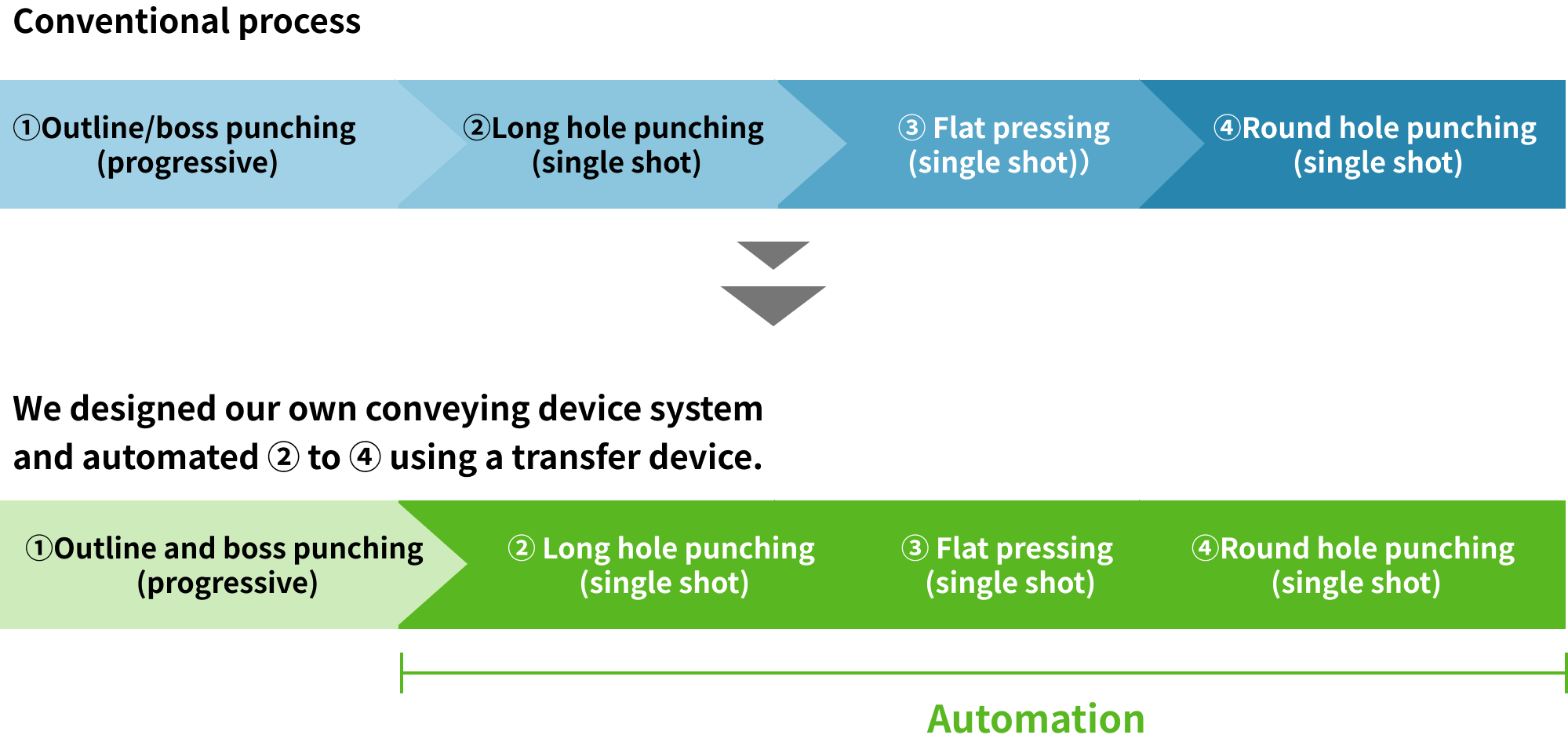
Product introduction: T company air conditioner parts
Material | SPHC |
Plate thickness | 4.3mm |
Narrow groove width | 2.0mm |
Production volume | 80,000 (pieces/month) |
Quality requirements
Groove width tolerance | SPHC |
Boss shape ①Positioning degree ②Backside bulge |
φ0.2 or less, 0.3 mm or less |
Flatness | 0.2 mm or less |
Improved punch durability | At start-up Currently Wear-out replacement after 300,000 pieces |
Breakage after 3,000 pieces
Meiko Technology 04
Multi-forming processing technology that reduces costs and improves production efficiency
Innovative processing technology with high efficiency and high yield
Our multi-forming processing is a next-generation processing technology that can handle complex shapes while reducing material waste. Short setup times and high-precision processing simultaneously reduce costs and improve production efficiency.
1. High yield with minimal material loss
By utilizing the material width for molding, scrap generation is significantly reduced. It can handle a wide range of expensive materials such as copper and aluminum, and can contribute to reducing material loss unmatched by other companies, especially for expensive materials.
2. Significantly reduced setup time
Servo motor drive makes it easy to change the setup of moving parts.Setup time reduced to 1/4 of the conventional time (from about 4 hours to about 1 hour).
3. Realization of complex shapes in one process
Complex shapes that required several processes in press processing can be handled in one process. Achieve cost reduction of up to 50%.
4. Flexibility due to servo motor drive
High-precision operation control is possible, and it can handle a variety of product shapes. The burden of setup changes is reduced, making it ideal for small lot and multi-product production.
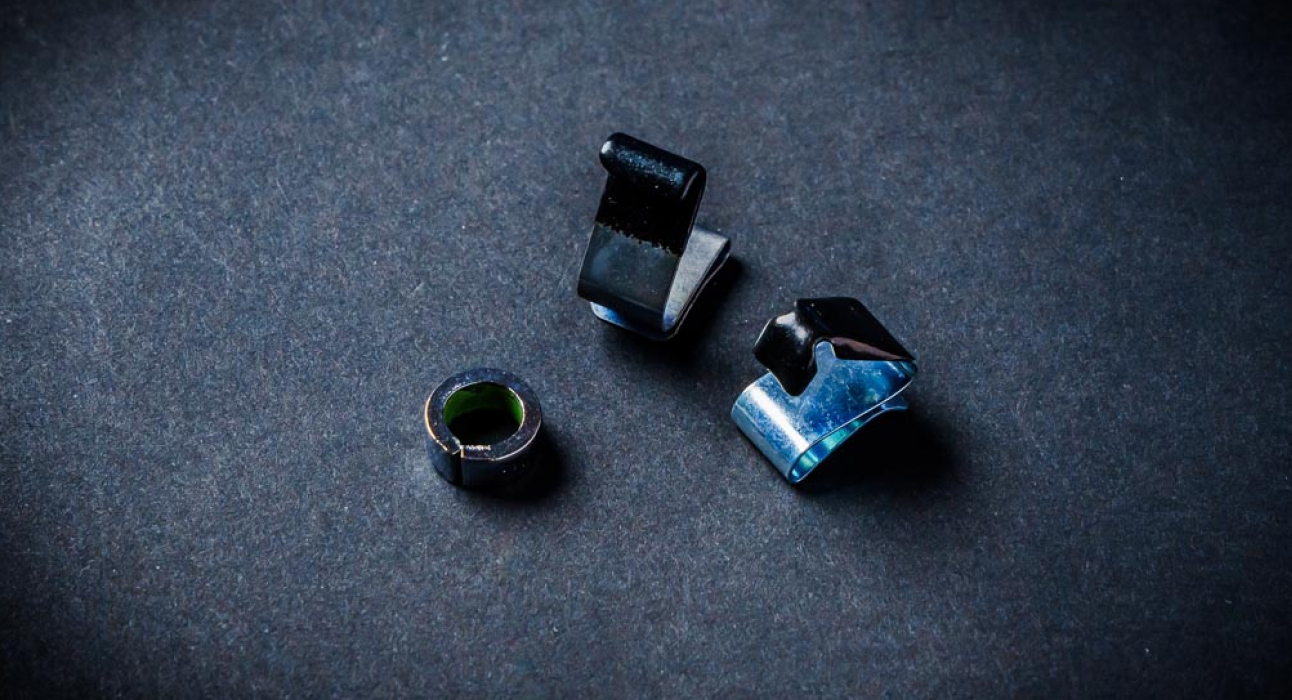
Next-generation busbar processing: Maximizing efficiency and cost-effectiveness with copper materials
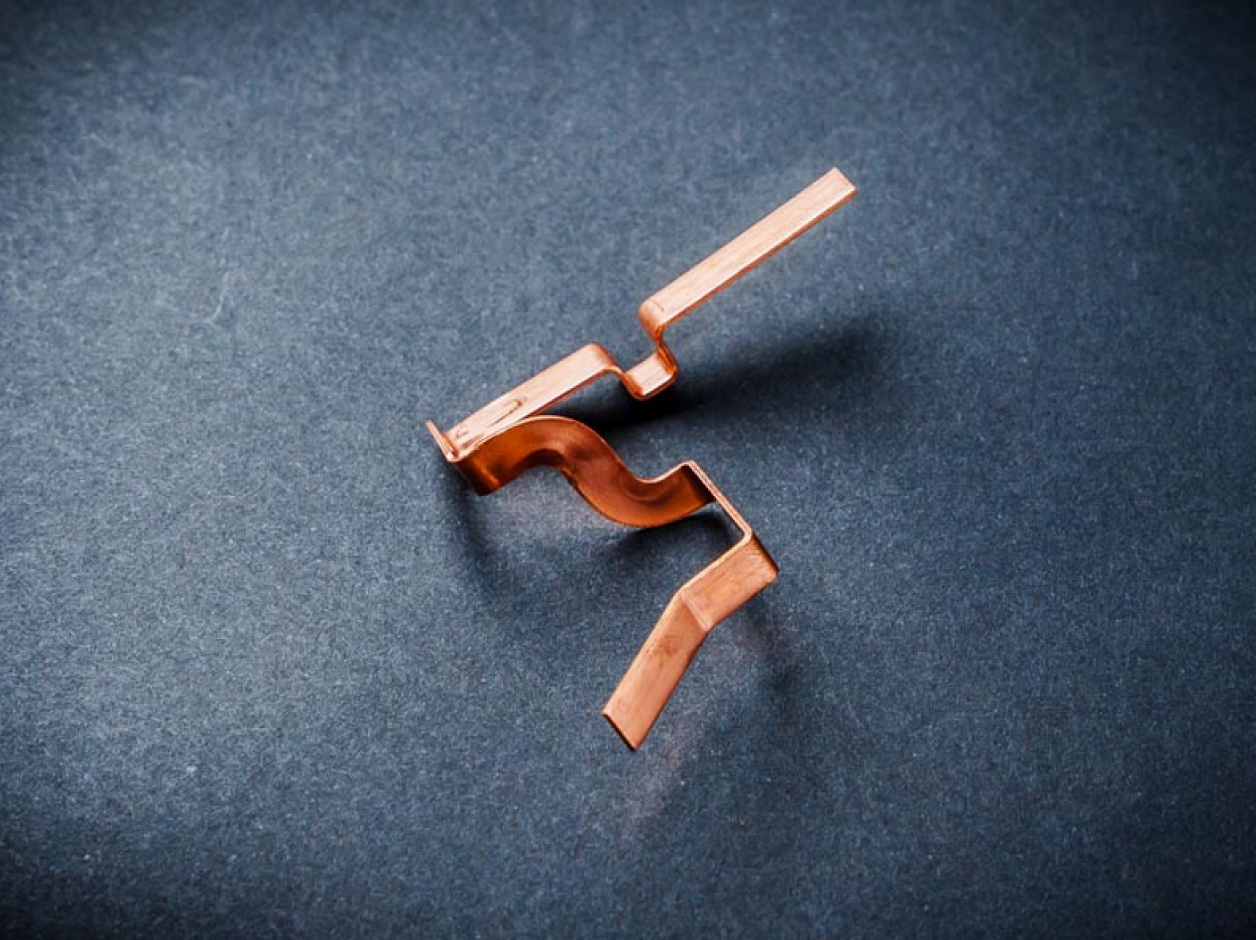
Our multi-forming processing is a next-generation processing technology that can handle complex shapes while reducing material waste. Short setup times and high-precision processing simultaneously reduce costs and improve production efficiency. In busbar processing using copper materials, multi-forming technology significantly reduces material loss and realizes efficient manufacturing.
By utilizing edgewise processing, shapes that were previously difficult can be handled. This simultaneously achieves cost reduction and environmental load reduction, providing great benefits especially for products using expensive copper materials.
1. Significant reduction in material loss
Since processing is possible with the material width = product width, excess material is eliminated and efficient processing is realized. "Edgewise processing" makes it possible to bend toward the material width side, which was previously difficult. This contributes to further reducing material loss.
2. Cost efficiency and environmental contribution
Significant cost reduction is possible, especially in processing copper materials. It also contributes to reducing CO2 emissions by reducing material, supporting sustainable manufacturing.
3. Great contribution to busbar products
Improve efficiency and cost performance in the processing of copper busbars. Provides great added value in fields that require high-precision processing without wasting materials.
4. Diverse response capabilities
Flexibly responds to complex shapes and special designs that are difficult to handle with press processing.
Needs tolerance adjustment
Tolerances may increase due to the accumulation of bending in each process.Supports careful adjustments from the design stage to realize high-precision product manufacturing.
Meiko Technology 05
Cost reduction through line design and construction using robots
Automation x efficiency = a new form of manufacturing created by robots
We have established a system in which we can consistently design and construct lines using robots in-house.
We can also design and manufacture simple equipment such as sorting machines, enabling us to build flexible and low-cost lines. This allows for short-term implementation and rapid start-up.
1. Labor saving through unmanned operation
We work with equipment manufacturers to automate tasks that previously required human labor. By using robots, we have significantly reduced the number of workers required.
2. Efficiency through process linkage
Our unique automated process design and joint technology with manufacturers allow us to efficiently link individual processes with robot technology. This optimizes the work flow, shortens operating hours, and stabilizes quality.
3. Cost reduction
In addition to efficiency and labor saving, we use robot technology to reduce long-term maintenance costs and reduce defective products. This reduces direct manufacturing costs and creates high economic benefits.
By designing automated processes using robots, we can work with equipment manufacturers to build flexible and highly efficient lines. This initiative comprehensively solves issues at the manufacturing site and contributes to improving the competitiveness of our clients.
MEIKO TECHNOLOGY 06
Low-cost, highly efficient line construction made possible by simple equipment
Increase efficiency at low cost! Total solution for simple equipment
Our company handles everything from designing to manufacturing simple equipment such as sorting machines and automatic box changers in-house. We can design and manufacture in a short period of time, and we can ensure smooth operation even after installation.In addition, we have specialized personnel in-house who are responsible for the design and manufacture of simple equipment, and we also focus on human resource development, so we aim to continuously evolve our technology.
1. Low-cost line construction
By introducing simple equipment manufactured in-house, we can provide high-quality products while keeping initial investments low. We can respond flexibly with short delivery times.
2. Contribution to cost reduction
By utilizing simple equipment to optimize the production process, we can reduce running costs and energy consumption. Efficient production can be achieved.
3. Flexible customization
We can design custom-made equipment according to the needs of each process. Our in-house specialized staff can handle the process and build a line optimized for your unique production conditions. We also provide education to improve the technical skills of staff working on-site, aiming for sustained improvement of technology.
We pursue "building a high-quality, flexible production line while keeping costs down," and realize human resource development and technological development.
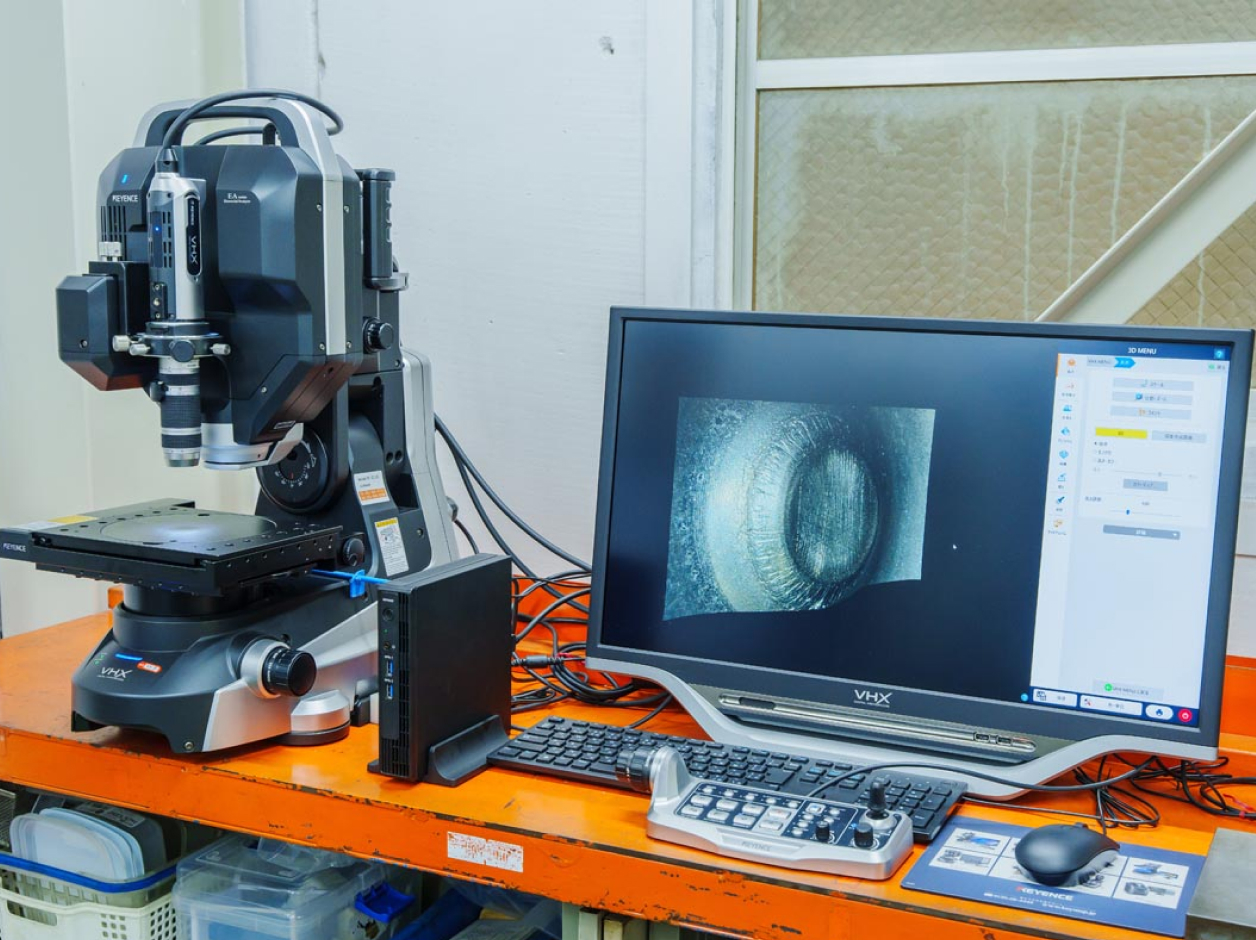
Meiko Technology 07
Innovation in quality with cutting-edge technology, Meiko Hatsujo's quality control
Our efforts in quality control
We improve product accuracy, prevent problems, and quickly resolve issues. We will continue to update our equipment and improve our technology to continue providing quality that our customers can trust.
1、About measurement
In order to thoroughly control the quality of springs, we have installed measuring machines similar to those in the measurement room on-site. This allows for high-precision measurements on-site and minimizes measurement errors.
In addition, by installing similar measuring machines at our major suppliers, we are able to share measurement data and respond quickly. This system strengthens quality assurance throughout the supply chain and delivers highly reliable products.
2、Contamination control/Elemental Analysis
We specialize in the management of contamination (foreign matter contamination) and are equipped with microscopes that can perform simple elemental analysis. This allows us to quickly and accurately inspect important parts, including brake part springs, for foreign matter.
This initiative contributes greatly to preventing quality problems in parts where safety is of particular importance.
1、Non-contact 3D measuring machine
High-precision 3D measurement is possible, and product dimensional inspection is carried out in a short time. This device is characterized by its ability to measure accurate dimensions while avoiding the effects of contact, even for products with complex shapes.
2、Whole 3D scanning measuring machine
Performs 3D scanning of the entire product to obtain detailed shape data. This scan data is compared with past measurement data and CAD data to identify subtle differences from the design and help improve product accuracy. It can also be used to inspect large parts and complex shapes.